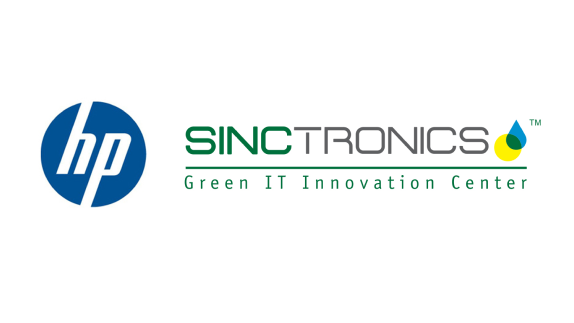
name:
HP Brazil & Sinctronics
The Need: an estimated 50 million tons of electronic equipment is discarded every year globally, a figure increasing 17% a year due to lack of reverse logistics and remanufacturing initiatives.
The Solution: combine HP’s outreach capacity to establish a robust reverse logistics scheme with Sinctronics’ capacity and expertise to recover and create value out of HP end-of-use electronic equipment.
What makes it circular? Design decisions happen in one company, while production is carried out by another - forming a partnership has been fundamental to create feedback, exchanging information on practical feasibilities that are key to increase circularity.
The Benefits: collection times reduced by 50%, costs reduced by up to 30%, and 97% of the collected materials and components reincorporated into Sinctronics’ supply chains.
The partnership between HP and Sinctronics has brought about the first circular economycircular economyA systems solution framework that tackles global challenges like climate change, biodiversity loss, waste, and pollution. It is based on three principles, driven by design: eliminate waste and pollution, circulate products and materials (at their highest value), and regenerate nature. initiative in the Brazilian electronics sector. HP has considerable manufacturing operations in Brazil and have set themselves a zero waste to landfill ambition through the adoption of a circular economy strategy. To help achieve this, HP has formed a partnership with Sinctronics, which has facilitated the development of processes to increase the volume of recycled materials into new products and packaging.
In 2008, Flex became the manufacturing partner of HP Brazil. Flex offer design, manufacturing, distribution and aftermarket services to original equipment manufacturers globally, and worked with HP Brazil to provide one facility to support the whole HP product portfolio in the country and improve efficiency and synergies in the supply chain.
Working side by side
The circular economy is driving a new approach to business around the world and will transform the way the economy produces and consumes goods and services. Flex and HP, as market leading companies, have embraced this idea as a way of creating value for their business, customers and society. From these common goals, Sinctronics was created in 2012 as the first unit of Flex to provide recycling solutions for the IT sector. The idea was to apply industrial standards and expertise into the recycling process, thereby scaling circular economy solutions. Sinctronics business objectives seek to generate value by providing a full portfolio of services and solutions that goes from a reverse logisticsreverse logisticsSupply chains dedicated to the reverse flow of products and materials for the purpose of maintenance, repair, reuse, refurbishment, remanufacture, recycling, or regenerating natural systems. management system to providing technology that helps incorporate recycled materials into new pieces and parts of IT products.
The creation of a Recycling and Innovation Center next to the manufacturing site was an important first step in understanding and re-thinking the product cycle. Cross-company communication allows for the most up to date knowledge on disassembly to be disseminated among all fields of expertise. It also enables Sinctronics to share practical insights with HP, seeking to influence and enhance their design decisions and identify new opportunities to create a closed loop process between manufacturing and recycling end-of-use products. For both companies, designing products and services that enable circular economy applications is a business opportunity. Sinctronics is committed to stimulating the development of recovered materials markets by using recycled content in new HP products.
The manufacturing of the future has already begun, and it has the potential to reduce the impact on the environment, create jobs and wealth at the same time.
- Carlos Ohde, Sr Director Innovation and New Ventures, Sinctronics
One of the specific goals of the partnership between HP and Sinctronics was the development of a closed loop process for plastics recovered from HP end-of-use products. After a lot of research and interaction between engineering and technical teams of both companies, the initiative achieved a breakthrough. The R&D process led to the development of recycled white plastic, to be used in electronics products, which satisfied the high-quality criteria and cosmetic appearance required by HP. The process to obtain the white plastic is very rigorous, as any contamination in the final recycled plastic will change the purity of the white colour required. The recycled white plastic used is made of at least 94% recycled plastic and up to 6% pigments and additives, to achieve the purity of 96% required by HP.
Raising ambition
The average level of recycled material in HP Brazil printing products, by plastic weight, is currently 30% and our goal for 2023 is to increase this to 45%, as part of the company's circular economy strategy. However, this will require an increase in the collection rates of end-of-use products or even the use of post-consumer plastics from other sectors. As well as reducing waste and creating added value, the strategy can also lead to environmental benefits such as a reduction in GHG emissions.
Through the program, 97% of materials collected by Sinctronics is now recovered to be directly returned into the supply chain. A proportion goes back into HP products while the remainder, for example materials such as metals, join other local supply chains. For HP, this outcome not only helps accomplish its circular economy goals but also bring costs reduction and less volatility across the supply chain. For Sinctronics, the project created an expertise in reverse logistics integrated into industrial strategy that can enable a decrease of its client costs up to 30% and in collection time for end-of-life products by 50%.
After bolstering capacity and understanding of the circular economy and an intensive R&D effort, Sinctronics can now provide the infrastructure and technology to collect and transform electronic waste into raw materials and components for new products.
As a business unit of global electronics manufacturer Flex, Sinctronics offers the first integrated ecosystem solution applying the concept of a circular economy to the electronics market in Brazil.
Flex set its sights on a circular economy in order to create a more comprehensive offering to OEMs, and as such began designing the ecosystem required for material recovery within client supply chains. This involved identifying the reverse logistics pillars required for the return of products to Sinctronics for recycling and reinsertion.
Flex had the manufacturing expertise and capabilities necessary to turn the idea of a circular economy for electronics in Brazil into a reality. Being a leading player in the electronics space, it could utilise intimate knowledge of manufacturing to dismantle equipment and feed its own supply chain. Respecting the need for independence and recognising that an organisation guided by creativity needs to innovate without restrictions or limitations, Sinctronics was created. The plan was to develop a complete ecosystem built on four pillars: reverse logistics, recycling facilities, research and development, and reverse supply chains.
This involved a significant engagement and capacity building effort. Internal processes needed to be created, new knowledge acquired and new training programmes developed around the circular economy. To find the best collaboration opportunities, the company brought suppliers closer to align on values and ensure they understood the direction in which Sinctronics was heading. Customers were another vital stakeholder to get on board, and the team worked both promote the circular economy, and in turn provided customers with assistance in communicating the concept further down the value chain. Finally, working with local government and universities helped disseminate understanding of circular economy; creating favourable environment for future circular economy activities.
One of the goals of the programme was to develop a closed loop for plastics recovered from electronic waste, and this came with challenges in materials purity and performance. For example, achieving a desired colour or durabilitydurabilityThe ability of a product, component or material to remain functional and relevant when used as intended. can be difficult when handling a mixture of end of use materials. To overcome this, Sinctronics R&D performed at three-step acceptance process, at each stage pushing the capabilities of their materials reprocessing:
The first closed loop was a notebook box handle, a product with low cosmetic and mechanical requirements
The second closed loop was a door flag, a product with low cosmetic requirements, but mechanical requirements on par with virgin material.
The third closed loop was a printer chassis, a product with high cosmetic and mechanical requirements
In closing the third loop, Sinctronics was able to achieve results believed to be impossible. Through the practices and processes, they were able to create a recycled white plastic for the client and gain approval for colour matching. The material mix is 94% recycled plastic and 6% master to assist with colour requirements. Internal feedback loops, strict regulation creation by the laboratory and adherence to implemented processes resulted in a 10-month journey to accomplish this achievement.
Through Sinctronics’ circular economy programme, 97% of recovered material is now returned directly into the supply chain, with some being fed back into Flex products, and materials such as metals joining other supply chains. Through the investment in reverse logistics, Sinctronics can reduce client costs by up to 30% and speed up collection times by 50%.
Sign up to our newsletter
Sign up for our monthly newsletter and make sure to tick the “Supply chain” box below to receive the latest updates on circular supply chains.