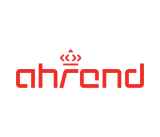
Overview
The challenge
Demand for office furniture is growing rapidly, by 2024, the size of the industry will be about USD 100 billion dollars. Manufacturing office furniture requires a lots of materials and energy and 80-90% of these valuable resources are lost after a short use period. How can the office furniture industry address rising demand in an increasingly resource constrained world?
The solution
Ahrend manufactures office furniture products with modularity, disassembly, and life extension as core design principles. In this way repairrepairOperation by which a faulty or broken product or component is returned back to a usable state to fulfil its intended use., upgrades, and modifications are easily achieved so that every single product can have multiple lives.
What makes it circular?
Ahrend offers their customers furniture-as-a-service (FAAS) where customers pay a monthly fee and return the furniture when they no longer need it.
What are the benefits?
A reduction in material usage and carbon emissions; closer relationships with customers, more profits, and a more secure materials supply chain; lower office set up costs and more flexibility in a fast-changing business environment.
The rising tide of white collar workers
Hundreds of millions of people around the world begin their day at the office by sitting down on their swivel chairs and resting their arms on their desks. With rising education levels and a growing service economy, the number of people starting their day like this will rise. Urbanisation and expanding global middle class, also contribute to the growth of ‘white collar’ employment. Combining these factors mean demand for office space and therefore office furniture will increase significantly in the next few decades.
A high material using sector
Like most industrial sectors, office furniture typically adheres to the linear model of production. Many of the materials in products today come from increasingly expensive finite sources. Cross-sector competition for resources combined with an increasingly volatile supply chain for pure and high quality materials, mean that there is likely to be a considerable raw material supply risk for office furniture manufacturers in the future.
Office furniture also requires the use of natural materials, mainly wood, which is in fact the highest material input for the sector. Although there are some emerging timber innovations that could increase durabilitydurabilityThe ability of a product, component or material to remain functional and relevant when used as intended. of wood (e.g. Accoya) or reduce the quantity of wood required (e.g. cross-laminates), because of the rapid growth in the sector, there is potential tension between wood supply for furniture and the critical importance of preserving forest ecosystems to address the climate crisis.
Recycling of materials from old furniture will not be enough on its own. Material recycling not only reduces purity and quality of materials, but also by breaking down products and components into their constituent materials, there is an associated loss in energy, labour, and other resources.
Fast turnover and mostly linear
Once office furniture falls out of use, through wear, tear, breakages or as a result of business relocations or closures, furniture typically enters the municipal waste stream, ending up either in landfill or incinerated for energy. According to European Federation of Furniture Manufacturers (UEA) statistics, in Europe as a whole, 80-90% of all furniture ends its life in this way.
This high turnover ‘fast furniture’ model is exceedingly wasteful in a material sense, with the result that a substantial amount of resources (energy, labour, water) embedded in products are lost at the point of disposal. The loss in value and associated negative environmental and social impacts, mean that there is a clear case to rethink office furniture design and delivery mechanisms.
A sector that is ready for change
Recognising future supply risks as well as the opportunities in shifting from the linear production and sales model, Dutch office furniture company Royal Ahrend has started to shift the sector onto a different trajectory by putting circular economycircular economyA systems solution framework that tackles global challenges like climate change, biodiversity loss, waste, and pollution. It is based on three principles, driven by design: eliminate waste and pollution, circulate products and materials (at their highest value), and regenerate nature. principles at the heart of their business.
Since the early 1990s, Ahrend have designed all of their furniture products with life extension in mind. Their manufacturing facilities have been configured for over 20 years, with stations and processes specifically designed to create modular products. Office chairs, tables, and other furniture move through the manufacturing facility with components added in sequential steps, like building a lego model. This facilitates more effective product maintenance, as well as upgrading with new parts, thus giving the best chance of conserving the embedded value in products, components, and material for as long as possible.
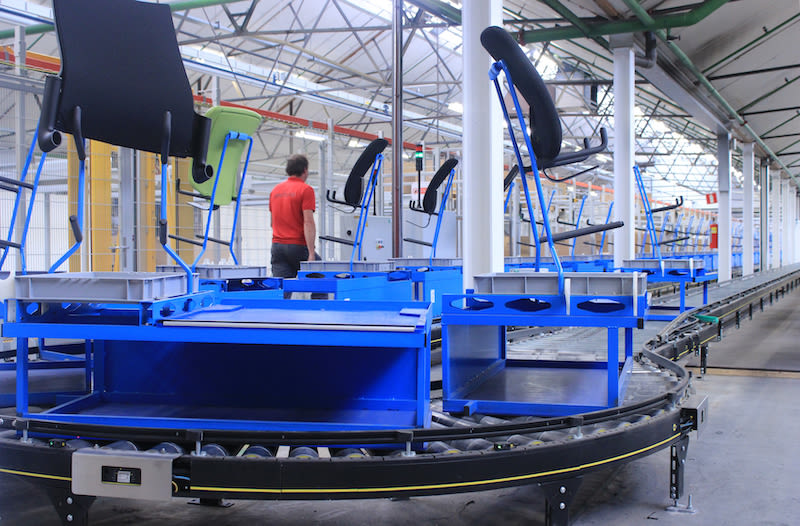
Ahrend has a fully modular production process
Supply chain engagement
Ahrend have not only shaped their manufacturing processes to create components and products fit for modularity, the company also insists that material suppliers and externally sourced components adhere to this model. When Ahrend develop a new product, many parties are invited to collaborate from the first day of the design process to drive innovation within the supply chain.
Successful projects so far have included a collaboration with KLM Airlines to provide old upholstery material along with component manufacturer PLANQ to provide expertise and facilities to break down the used fabrics and transform them into durable table top surfacing materials. A more recent collaboration involved Ecor and DSM, two other members of the CE100 network, providing 100% modular and reusable desktops manufactured with cellulosic waste and DSM-Niaga’s non-toxic reversible glue. The potential impact is significant. Based on an annual production of 150,000 desks, such a collaboration could save the extraction of 2250 tonnes of virgin timber from carbon-sequestering woodland.
Furniture as a service (FAAS)
Innovative manufacturing processes and use of high performance recycled materials are great design strategies through which Ahrend has created circular products. The next ambition level is to reshape their entire business model, to ensure that the benefits of life extension can be realised. Under a traditional transactional model, products are sold to other businesses, but there is no way of knowing what happens to them next. If the business model changes so that Ahrend remains owner, the company can ensure materials and the embedded resources are conserved.
With this in mind, in the last few years, Ahrend established the very first Furniture As A Service (FAAS) model, with the Ellen MacArthur Foundation as the very first customer. Unlocking the potential of the new 'circular use agreement' relied on a number of important enablers:
Technology - the inclusion of QR codes on products, along with a new internal database, has allowed Ahrend to continually log, store, and track the history of all assets under their ownership. This ensures a smooth flow of information on the quality and health of their products, and important datasets to enable the scaling and management of the FAAS model.
Financing - the creation of an alternative financing model has provided the flexibility and experimental space needed for the FAAS model to work. Ahrend is private equity owned, allowing the business to create a separate financial entity called Circular Interiors that owns the products. This allows Ahrend, the furniture company, to free themselves from certain financial constraints, such as the need to generate short-term returns, which can often limit companies from piloting and implementing similar access-over-ownership business models.
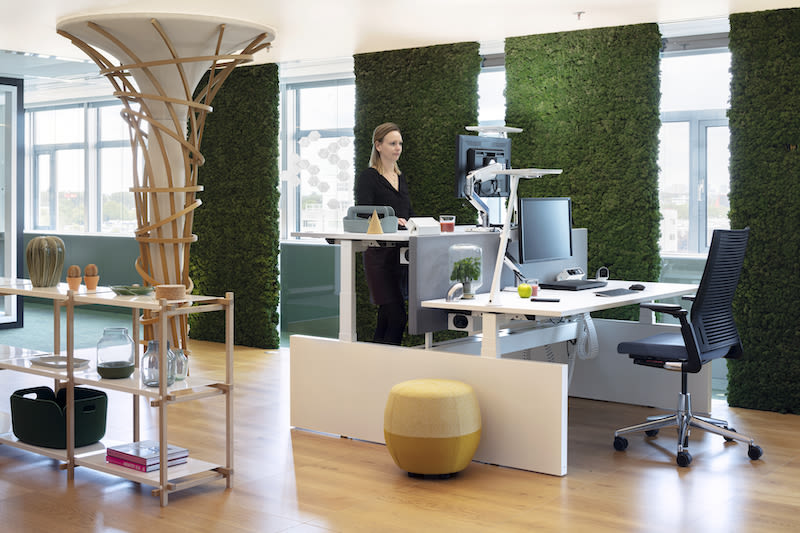
FAAS protects Ahrend's future material supply chain and offers customers more flexibility.
The obstacles that were overcome
There are a number of lessons that can be learnt from Ahrend’s journey in scaling up the first FAAS offering in Europe.
Firstly, the potential benefits of capturing value and mitigating supply risks through FAAS were not widely appreciated in the Netherlands when Ahrend introduced the new option to customers. Today, we see far more awareness about circular economy and material reusereuseThe repeated use of a product or component for its intended purpose without significant modification. advantages at various levels. Ahrend have found that as the key players in the value chain have come to understand the rationale of the FAAS option, the easier it has become to form the necessary partnerships, contract new customers, and bring the model to scale.
Another challenge related to the establishment of the reverse logistics infrastructure needed for the business model to be successful. As reverse logisticsreverse logisticsSupply chains dedicated to the reverse flow of products and materials for the purpose of maintenance, repair, reuse, refurbishment, remanufacture, recycling, or regenerating natural systems. systems have matured over the last decade in the Netherlands, the viability of the FAAS model has increased. Ahrend only offers FAAS in and around the Netherlands (and to the Ellen Macarthur Foundation), because they want to understand the challenges in one small area, before scaling up into other regions of Europe.
The final barrier that Ahrend needed to overcome, was the significant internal resistance in bringing the FAAS option to life. Convincing various departments that the company’s future direction lay in leasing furniture rather than selling it outright, took considerable time and effort, including developing the business case that such an approach would work in the long term. Once internal buy-in was achieved, internal digital and physical infrastructure needed to be adapted - particularly in the production facilities - to ensure systems were prepared for the return of products from customers.
Multiple benefits across the board
By definition, the design of long lasting furniture delivered via a circular business model will create advantages and benefits to business, customers, and society more broadly.
The main benefit of FAAS is the reduced need for virgin materialsvirgin materialsMaterials that have not yet been used in the economy., which directly correlates to less energy use, reducing carbon emissions and other environmental impacts related to material extraction and processing. As an indication of potential material savings, Ahrend sold 150,000 desk chairs in 2018, which in total comprises 2,400 tonnes of material. During a 30 year period, including periodic upgrades of wheels, control mechanisms, textiles, and other components, the potential material savings from keeping such a chair in use, compared to the manufacture, use and disposal of three ‘standard’ desk chairs, could total more than 4,000 tonnes.
In terms of business benefits, FAAS means Ahrend can have a closer relationship with customers and there is potential for greater profits. If the desk or chair can be maintained in use for more than about 5 - 6 years, from that point on, the revenue per item is increased compared to a straight sale. Also as Ahrend maintains ownership of the furniture, many of the recovered components and materials can be used to make the next chair, thus reducing future manufacturing costs and fulfilling Walter Stahel’s famous observation that: “the products of today are the materials of tomorrow at yesterday’s prices”.
Finally, Ahrend customers can benefit through greatly reduced office set-up costs, as well as an increased ability to stay lean and agile, particularly advantageous if in the startup phase or in a fast-moving industry. For larger business customers, leasing rather than owning furniture reduces the level of asset-management required within its operations. If they have left over furniture in one facility, Ahrend can match it with demand in another facility. In general, the FAAS model gives clients more flexibility around planning cycles which are usually 5-8 years (for example, due to changing work force and new ways of working), while furniture easily lasts longer. This flexibility allows FAAS customers to have an up-to-date interior design that fits the needs of the brand and the employees, avoiding the need for storage or production of waste as situations change.
All of this suggests that circular economy thinking is the bright choice for an office furniture industry that can work in the long term.