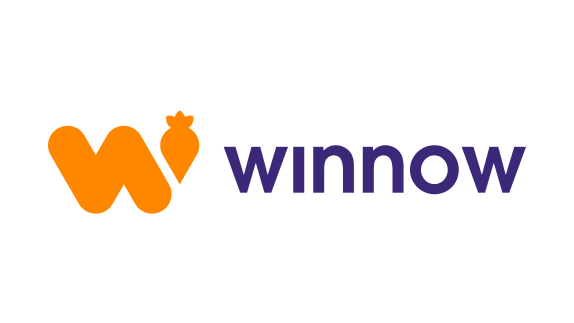
In a typical commercial kitchen, up to 20% of all food purchased is thrown away, leading to lost profits, wasted resources and numerous social and environmental impacts. Responding to this, Winnow has created an easy-to-install technology that collects data and generates insights on food waste.
Winnow’s clients include hotels, casinos, retailers, healthcare providers, contract caterers and cruise ships. A competitive marketplace, combined with rising food prices, means that most of these business sectors are very receptive to ways of becoming more efficient.
How does Winnow enable the circular economy?
Winnow was founded with a simple belief that food is too valuable to waste.
According to the UN, up to a third of all food that is produced in the world is lost or wasted, with an estimated value of USD 1 trillion discarded each year. Furthermore, greenhouse gas emissions from decomposition of post-consumer organic waste is responsible for 5% of global emissions. The elimination of food waste is a cornerstone of a circular economycircular economyA systems solution framework that tackles global challenges like climate change, biodiversity loss, waste, and pollution. It is based on three principles, driven by design: eliminate waste and pollution, circulate products and materials (at their highest value), and regenerate nature. for food.
By providing an easy way to weigh, categorise and analyse the underlying reasons for food waste, Winnow’s technology increases awareness in kitchen staff, facilitating better decision making in menu design and food preparation, so that less food is thrown away.
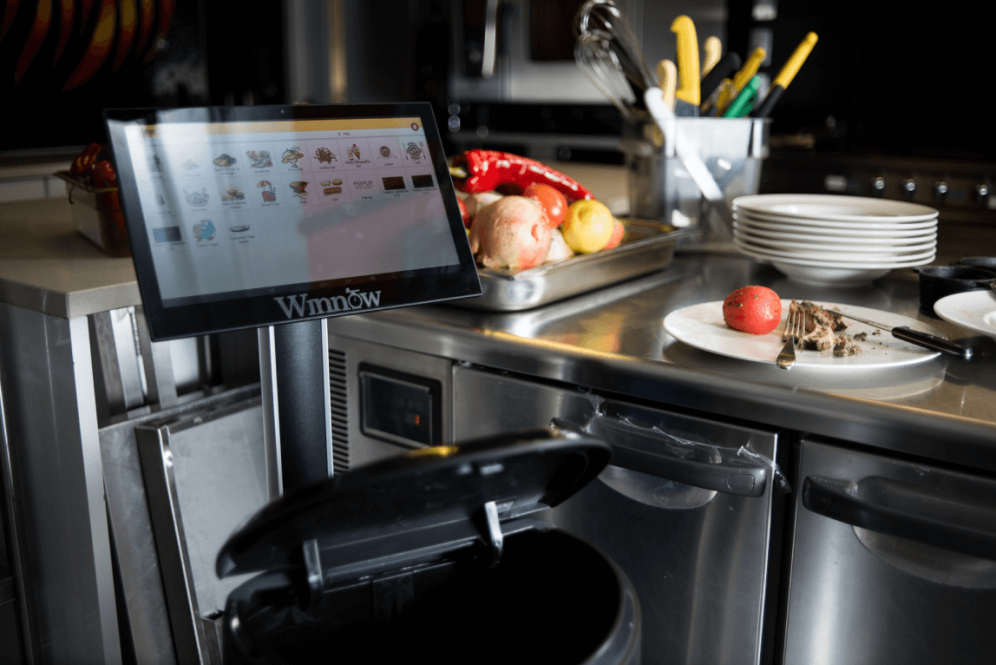
Image credit: Chris King
How does Winnow work?
Winnow technology comprises a weighing scale installed under the kitchen waste bin and a method of identifying the type of food that is being discarded. Depending on the size of the kitchen and nature of the operation, Winnow offers two modes of identification:
Winnow Vision is an AI-powered system for larger kitchens. Each time food is placed in the bin, the system logs the weight and a camera mounted over the bin automatically identifies the food type.
Winnow Track is a system for small businesses or where there are fewer varieties of food that are potentially discarded. Each time food is dumped in the bin, the food is weighed and a staff member manually identifies the food type on a touchscreen display.
The true value of the system lies in the analytics generated on daily and weekly intervals and, for larger companies, across multiple sites. Winnow’s revenue model is based on sending out these regular reports, for which it charges a monthly service fee tiered according to the size (in terms of total food costs) of the kitchen.
In the first few weeks of the analysis period, clients are requested to collect data without modifying behaviour, to establish a baseline for future comparison. The key outputs are a function of the weight of the food type and the timestamp when this weight was recorded. To add more meaning to this basic measurement, Winnow requests information on food sales during the same time period, so that waste can be normalised against sales, creating a more powerful metric that can be related to return on investment and profits. The analysis also provides other useful estimates, including the volume of avoided carbon emissions.
Benefits
The first insight experienced by many clients during the baselining period is that food waste is typically underestimated by a factor of two, leading to imprecise forecasting and financial planning.
Once the baseline is established and the analysis period begins, a typical client can expect to reduce waste by 40 - 70%, with an average reduction of about 50%. In the hospitality industry where margins are typically low, this scale of reduction could lead to a doubling of profits in many businesses.
Less than a decade after its launch, Winnow technology now serves more than 1,400 businesses across the world, saving the equivalent of 36 million meals each year from the bin. The corresponding economic and environmental benefits include:
USD 43 million in food cost savings for its clients
61,000 tonnes of CO2e prevented per year
4.4 billion litres of water that would have otherwise been wasted